To troubleshoot a Honeywell gas valve, check for proper voltage supply and ensure the valve is not stuck. Verify the thermostat settings and gas supply.
Honeywell gas valves are critical components in heating systems, controlling the flow of gas to the burner. Regular maintenance and troubleshooting are essential for safe and efficient operation. Common issues include improper voltage, stuck valves, and incorrect thermostat settings. Addressing these problems promptly ensures your heating system runs smoothly.
Always prioritize safety by turning off the gas supply before performing any checks. Understanding basic troubleshooting steps can save time and prevent costly repairs. This guide provides practical tips to diagnose and fix common Honeywell gas valve issues effectively.
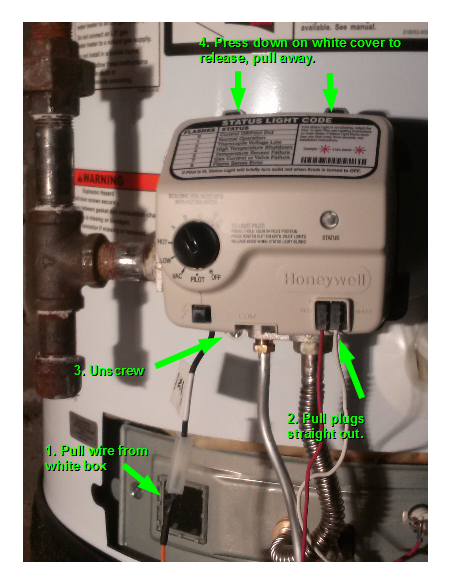
Credit: tylertork.com
Introduction To Honeywell Gas Valves
Honeywell gas valves play a crucial role in various heating systems. They ensure safe and efficient fuel delivery to your appliances. Understanding these valves can help you troubleshoot common issues.
Importance Of Gas Valves
Gas valves are essential for controlling the flow of gas. They maintain the right pressure and keep your systems running smoothly. Safety is the primary function of gas valves. They prevent gas leaks and potential hazards.
Efficiency is another key aspect. Properly functioning gas valves ensure optimal fuel usage. This helps in reducing energy bills and maintaining a sustainable environment. Regular maintenance of gas valves can prevent unexpected breakdowns.
Common Applications
Honeywell gas valves are used in various systems. They are common in residential heating systems. You will find them in boilers, furnaces, and water heaters. In commercial settings, they are used in large-scale heating systems.
Industrial applications also rely on these gas valves. They are used in manufacturing plants and processing industries. Their versatility makes them suitable for a wide range of applications.
Application | Example |
---|---|
Residential Heating | Boilers, Furnaces, Water Heaters |
Commercial Heating | Large-scale Heating Systems |
Industrial Use | Manufacturing Plants, Processing Industries |
Knowing the applications can help in proper troubleshooting. It ensures the right steps are taken for each system.

Credit: m.youtube.com
Identifying Common Issues
Honeywell gas valves are known for their reliability. Yet, they can still face issues over time. Identifying these problems early can save you time and money. This guide will help you understand common problems and how to spot them.
Signs Of Malfunction
Recognizing the signs of malfunction is crucial. Here are some common indicators:
- Burner won’t ignite: The gas valve might be faulty.
- Strange noises: Hissing or clicking sounds can indicate issues.
- Pilot light issues: A weak or flickering pilot light is a red flag.
- Gas smell: This is a serious issue. Turn off the gas and call a professional.
These signs can help you determine if your Honeywell gas valve needs attention.
Frequent Error Codes
Honeywell gas valves often display error codes. Knowing these codes can make troubleshooting easier. Here are some common ones:
Error Code | Meaning |
---|---|
ERR01 | Valve not responding |
ERR02 | Low gas pressure |
ERR03 | Flame sensor fault |
ERR04 | Overheating detected |
Understanding these codes can help you diagnose and fix issues quickly. Always refer to the manual for detailed information.
Basic Troubleshooting Steps
Having trouble with your Honeywell gas valve? Follow these basic troubleshooting steps. They help you identify and fix common issues quickly. Let’s dive into the steps to get your gas valve working again.
Initial Inspections
Start with a visual inspection. Ensure the gas valve is clean and free of debris. Check for any visible signs of damage or wear.
- Inspect the wiring connections: Make sure all wires are secure and undamaged.
- Check for leaks: Use a gas leak detector or soapy water. Look for bubbles forming around the valve.
- Verify the power supply: Ensure the gas valve is receiving power. Check the circuit breaker and any fuses.
Simple Fixes
Sometimes, simple fixes can resolve the issue. Follow these steps to try quick solutions:
- Reset the gas valve: Turn off the power for a few minutes, then turn it back on.
- Adjust the thermostat: Make sure the thermostat is set to the desired temperature.
- Clean the filter: A dirty filter can affect gas valve performance. Clean or replace it if necessary.
If these steps don’t solve the problem, further diagnosis may be required. Consult a professional for more complex issues.
Advanced Troubleshooting Techniques
Troubleshooting a Honeywell gas valve can be complex. Advanced techniques can help you diagnose and fix issues effectively. These methods use diagnostic tools and interpreting results accurately.
Using Diagnostic Tools
Diagnostic tools are essential for advanced troubleshooting. They help identify specific problems in your Honeywell gas valve. Here are some common tools used:
- Multimeter: Measures voltage, current, and resistance.
- Manometer: Checks gas pressure.
- Thermocouple tester: Tests thermocouples for functionality.
Using a multimeter:
- Set the multimeter to the correct measurement mode.
- Connect the probes to the appropriate points on the valve.
- Read the values displayed on the multimeter.
Using a manometer:
- Attach the manometer to the gas valve’s pressure port.
- Turn on the gas supply and read the pressure.
- Compare the reading with the manufacturer’s specifications.
Using a thermocouple tester:
- Connect the thermocouple to the tester.
- Heat the thermocouple tip with a flame.
- Observe the tester’s reading for proper function.
Interpreting Results
Interpreting the results from your diagnostic tools is crucial. This ensures you pinpoint the exact issue. Below are some guidelines:
Multimeter readings:
Measurement | Expected Range |
---|---|
Voltage | 24V AC |
Resistance | 10-50 ohms |
If the voltage is below 24V, check the power supply. If resistance is outside the range, the valve may be faulty.
Manometer readings:
- Read the gas pressure carefully.
- Compare it with the manufacturer’s specifications.
- Adjust the pressure regulator if needed.
Thermocouple tester results:
- Ensure the thermocouple generates a small voltage when heated.
- If no voltage is generated, replace the thermocouple.
Accurate interpretation of these results will guide you to the correct fix. Always refer to the Honeywell manual for specific guidelines.
Maintenance Tips
Maintaining your Honeywell gas valve ensures safety and efficiency. Regular checks and preventative measures extend the valve’s lifespan. Below are some maintenance tips to keep your gas valve in top shape.
Regular Checks
Performing regular checks on your Honeywell gas valve is crucial. Inspect the valve for any visible damage or wear. Look for signs of corrosion, dirt, or debris. Make sure the valve operates smoothly.
Create a maintenance schedule to check the valve monthly. Use a checklist to ensure you don’t miss any steps. Here is a sample checklist:
- Inspect for visible damage
- Check for corrosion
- Ensure smooth operation
- Listen for unusual noises
Preventative Measures
Taking preventative measures can prevent major issues. Clean the valve regularly to remove dust and debris. Lubricate the moving parts to ensure smooth operation.
Here are some preventative measures to follow:
- Clean the valve monthly
- Lubricate moving parts
- Check for gas leaks
- Replace worn-out parts
Table of Preventative Measures:
Measure | Frequency |
---|---|
Clean the valve | Monthly |
Lubricate parts | Every 3 months |
Check for leaks | Monthly |
Replace parts | As needed |
When To Call A Professional
Sometimes, fixing a Honeywell gas valve might be too hard. Calling a professional can save you time and trouble. Here’s when you should call for expert help.
Recognizing Complex Issues
Understanding when a problem is too complex is crucial. Complex issues may include:
- Gas leaks
- Valve not opening
- Unusual noises
These problems need specialized tools and knowledge.
Selecting A Qualified Technician
Choosing the right technician is important. Follow these steps to find a qualified technician:
- Check certifications
- Read reviews
- Ask for references
Ensure they have experience with Honeywell gas valves.
Safety Precautions
Handling Honeywell gas valves requires strict adherence to safety precautions. These steps ensure your safety and the proper functioning of the valves. Below, we discuss the key safety measures to follow during troubleshooting.
Handling Gas Valves Safely
Always turn off the gas supply before you start. Ensure the area is well-ventilated to avoid gas accumulation. Use proper tools and wear protective gloves to prevent injuries.
- Turn off the gas supply before troubleshooting.
- Ensure the area is well-ventilated.
- Wear protective gloves and use proper tools.
Emergency Procedures
Know the emergency procedures in case of a gas leak. Evacuate the area immediately if you smell gas. Do not operate electrical devices. Call emergency services from a safe location.
- Evacuate the area immediately if you smell gas.
- Do not operate any electrical devices.
- Call emergency services from a safe location.
Here is a quick reference table for emergency contacts:
Contact | Phone Number |
---|---|
Local Fire Department | 911 |
Gas Company Emergency Line | 800-123-4567 |
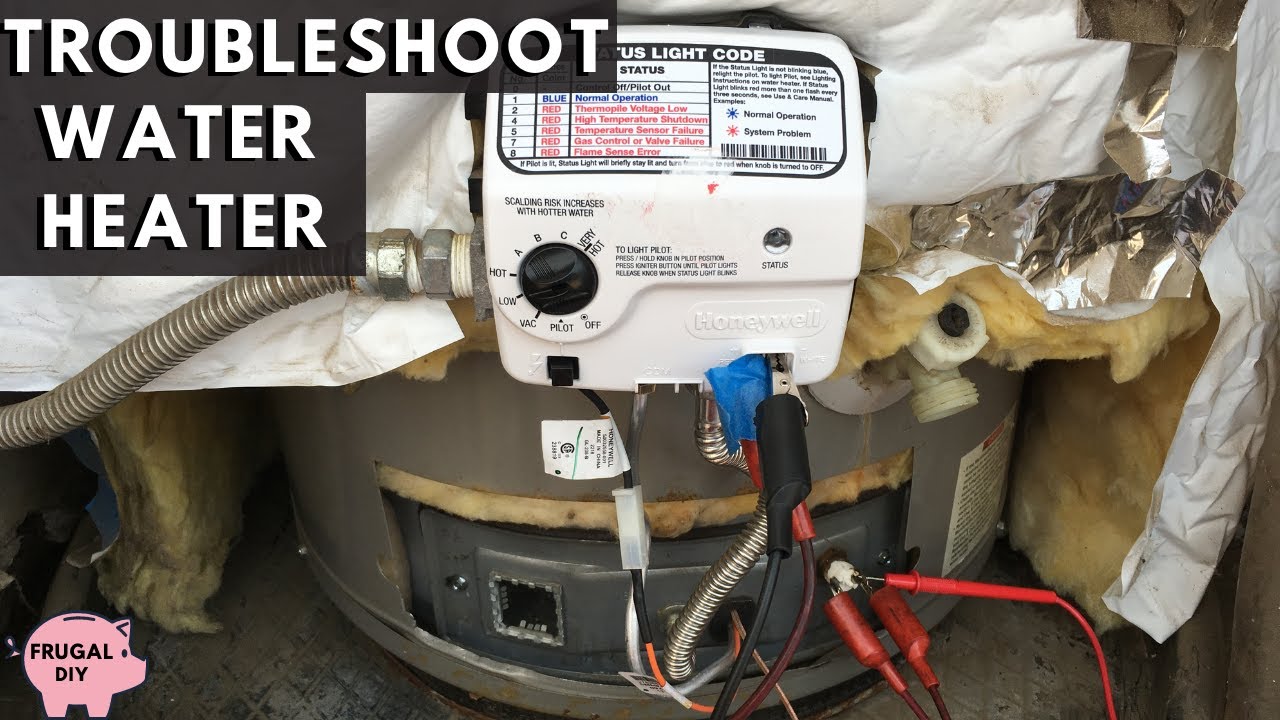
Credit: m.youtube.com
Frequently Asked Questions
How Do I Know If My Gas Control Valve Is Bad?
A faulty gas control valve may cause inconsistent heating, frequent pilot light outages, or strange noises. Check for these signs.
How To Diagnose Honeywell Gas Valve?
To diagnose a Honeywell gas valve, check for proper voltage, inspect wiring connections, test for gas leaks, and ensure the valve opens and closes correctly. Use a multimeter to verify electrical continuity and consult the valve’s manual for specific troubleshooting steps.
How Do I Reset A Honeywell Gas Control Valve?
To reset a Honeywell gas control valve, turn the knob to “Off. ” Wait 5 minutes. Turn it to “Pilot. ” Hold the reset button and light the pilot. Keep holding the button for 30-60 seconds. Release the button and turn the knob to “On.
“
Why Is My Gas Valve Not Working?
Your gas valve might not work due to a faulty thermocouple, power issues, or a clogged valve. Check for gas supply interruptions and ensure connections are tight. If problems persist, consult a professional for a thorough inspection and repair.
Conclusion
Troubleshooting your Honeywell gas valve can save time and money. Follow the steps for a safe and efficient solution. Regular maintenance ensures your system runs smoothly. Don’t hesitate to consult a professional for complex issues. Keep your home safe and your equipment in top condition.