First, check for error codes on the display panel. Then, ensure the machine is properly cleaned and maintained.
Taylor ice cream machines are popular for their efficiency and reliability. Despite this, they may occasionally encounter issues requiring troubleshooting. Common problems include error codes, inconsistent ice cream texture, and freezing issues. Regular cleaning and maintenance can prevent many of these problems.
Identifying the specific error code on the display can guide you to the appropriate solution. Always refer to the user manual for detailed instructions. Ensuring the machine is well-maintained can help extend its lifespan and ensure smooth operation. Proper troubleshooting can save time and reduce downtime, keeping your business running smoothly.
Common Issues
Owning a Taylor ice cream machine can be a delight. Yet, it’s not uncommon to face some challenges. Understanding common issues can save time and effort. Below are some of the frequent problems and their solutions.
Machine Not Freezing
One common issue is the machine not freezing properly. This could be due to various reasons:
- Insufficient Refrigerant: Check for leaks and refill refrigerant.
- Dirty Condenser: Clean the condenser regularly to ensure efficiency.
- Incorrect Mix: Use the recommended mix for best results.
Regular maintenance can prevent freezing issues. Ensure all parts are clean and functioning.
Unusual Noise
Another common problem is unusual noise from the machine. This might indicate:
- Loose Parts: Tighten any loose components.
- Worn Bearings: Replace any worn-out bearings.
- Motor Issues: Inspect the motor for any defects.
Always address unusual noises promptly. Ignoring them can lead to bigger issues.
Issue | Possible Cause | Solution |
---|---|---|
Machine Not Freezing | Insufficient Refrigerant | Check for leaks and refill refrigerant. |
Machine Not Freezing | Dirty Condenser | Clean the condenser regularly. |
Unusual Noise | Loose Parts | Tighten loose components. |
Unusual Noise | Worn Bearings | Replace worn-out bearings. |
Keep your Taylor ice cream machine in top condition by addressing these common issues. Routine checks and maintenance are key to smooth operation.
Basic Maintenance
Maintaining your Taylor Ice Cream Machine is essential. It ensures your machine runs smoothly and lasts longer. Basic maintenance involves regular cleaning and proper lubrication. Following these steps can prevent common issues and keep your machine in top condition.
Regular Cleaning
Regular cleaning of your Taylor Ice Cream Machine is crucial. It helps to prevent bacteria buildup and ensures the best-tasting ice cream. Follow these steps for effective cleaning:
- Turn off and unplug the machine.
- Disassemble all removable parts.
- Wash parts with warm, soapy water.
- Rinse thoroughly and let them dry.
- Use a soft brush for hard-to-reach areas.
- Clean the machine’s exterior with a damp cloth.
Cleaning frequency varies based on usage. Daily cleaning is recommended for high-usage machines.
Lubrication Tips
Proper lubrication is key to the smooth operation of your Taylor Ice Cream Machine. It reduces wear and tear on moving parts. Follow these lubrication tips:
- Use food-grade lubricant only.
- Lubricate all moving parts weekly.
- Focus on the drive shaft and o-rings.
- Apply a thin, even layer of lubricant.
- Reassemble the machine carefully.
Part | Lubrication Frequency |
---|---|
Drive Shaft | Weekly |
O-Rings | Weekly |
Regular lubrication extends the life of your machine’s components. Always follow the manufacturer’s guidelines for best results.
Error Codes
Taylor Ice Cream Machines are reliable but can sometimes show error codes. Understanding these codes helps fix the issues quickly. This section will guide you through some common error codes and their solutions.
Understanding Codes
Error codes are essential for troubleshooting your Taylor Ice Cream Machine. Each code indicates a specific problem. Knowing what each code means can save time and prevent bigger issues.
Error Code | Description | Possible Solution |
---|---|---|
E1 | High Temperature | Check the cooling system |
E2 | Low Temperature | Inspect the thermostat |
E3 | Motor Overload | Reduce the load |
Resetting The Machine
Sometimes, a simple reset can solve the problem. Follow these steps to reset your Taylor Ice Cream Machine:
- Turn off the machine.
- Unplug it from the power source.
- Wait for 5 minutes.
- Plug it back in and turn it on.
If the error code persists, you may need to consult the user manual or contact customer support.
Power Problems
Experiencing power problems with your Taylor ice cream machine can be frustrating. These issues can stop your business operations. Understanding how to troubleshoot power issues can save time and money.
Checking Connections
First, check all power connections. Ensure the machine is plugged in properly. Look at the power cord. Is it damaged? If so, replace it. Check the outlet. Plug another device into it. Does it work? If not, the outlet may be faulty.
Inspect the circuit breaker. Has it tripped? If yes, reset it. Make sure the voltage matches the machine’s requirements. Use a multimeter to verify. Incorrect voltage can cause power problems.
Step | Action |
---|---|
1 | Check power cord for damage |
2 | Test outlet with another device |
3 | Reset the circuit breaker |
4 | Verify voltage with a multimeter |
Power Cycling
Power cycling can resolve many issues. Turn off the machine. Unplug it from the outlet. Wait for 5 minutes. This allows the machine to reset. Plug it back in and turn it on.
Check if the machine powers up. If not, repeat the steps. Make sure to follow the manufacturer’s instructions. Avoid frequent power cycling. It can harm the machine’s components.
Power cycling works for many electronic devices. Taylor ice cream machines are no exception. It’s a simple and effective troubleshooting step.
By following these steps, you can fix many power issues. Keep your ice cream machine running smoothly.
Temperature Control
Maintaining the right temperature is crucial for your Taylor Ice Cream Machine. Proper temperature control ensures smooth, creamy ice cream and prevents spoilage. Follow this guide to troubleshoot and adjust the temperature settings effectively.
Adjusting Settings
First, check your machine’s temperature settings. Adjusting these settings can solve many problems. Here’s how:
- Locate the control panel.
- Press the temperature button to view current settings.
- Use the up and down arrows to adjust the temperature.
Ensure the temperature is set between 16°F and 20°F for optimal performance. If the ice cream is too soft or hard, tweak the settings slightly.
Calibrating Thermostat
A poorly calibrated thermostat can cause temperature fluctuations. Follow these steps to calibrate it:
- Turn off the machine.
- Open the access panel to locate the thermostat.
- Use a thermometer to check the current temperature.
- Adjust the thermostat dial to match the thermometer reading.
- Turn the machine back on and check the temperature again.
Repeat this process until the thermostat is accurately calibrated. This ensures consistent ice cream quality and prevents freezing issues.
Problem | Possible Cause | Solution |
---|---|---|
Ice cream too soft | Temperature too high | Lower the temperature setting |
Ice cream too hard | Temperature too low | Raise the temperature setting |
Machine not freezing | Thermostat miscalibration | Calibrate the thermostat |
Remember, regular maintenance of your Taylor Ice Cream Machine is key. Keep an eye on the temperature settings and calibrate the thermostat as needed.

Credit: www.partsfps.com
Mix Consistency
Maintaining the mix consistency in your Taylor Ice Cream Machine is crucial for producing high-quality ice cream. Proper mix consistency ensures your ice cream is smooth and creamy. Below, we’ll explore the essential aspects of maintaining mix consistency, focusing on Proper Mixing and Preventing Over-Aeration.
Proper Mixing
Proper mixing is key to achieving the right ice cream texture. Follow these steps to ensure your mix is well-blended:
- Check the mix temperature: Ensure the mix is at 40°F (4°C).
- Use fresh ingredients: Always use fresh milk and cream.
- Follow the recipe: Stick to the recommended ingredient ratios.
- Avoid lumps: Stir the mix until smooth and lump-free.
A well-mixed base guarantees consistent ice cream quality. It prevents issues like clumping and uneven freezing.
Preventing Over-aeration
Over-aeration can ruin the texture of your ice cream. Here are some tips to prevent it:
- Monitor the overrun: Keep the overrun within 30%-50%.
- Check the dasher speed: Ensure the dasher spins at the correct speed.
- Inspect the seals: Make sure all seals are intact to avoid air leaks.
- Regular maintenance: Clean and maintain your machine regularly.
By preventing over-aeration, you ensure a creamy and dense ice cream texture. This enhances the overall customer experience.
Aspect | Key Points |
---|---|
Proper Mixing | Check temperature, use fresh ingredients, follow the recipe, avoid lumps |
Preventing Over-Aeration | Monitor overrun, check dasher speed, inspect seals, regular maintenance |
By focusing on Proper Mixing and Preventing Over-Aeration, you can maintain the ideal mix consistency. This ensures your Taylor Ice Cream Machine produces the best ice cream every time.
Part Replacements
Maintaining your Taylor Ice Cream Machine involves routine part replacements. Keeping your machine in good condition ensures smooth operation and delicious ice cream. This section will guide you through identifying worn parts and sourcing replacements.
Identifying Worn Parts
Regularly inspect your Taylor Ice Cream Machine for any worn parts. Look for cracks, leaks, or unusual noises. Common parts that need replacement include:
- Seals
- O-rings
- Gaskets
- Blades
Check the condition of these parts during cleaning. Replace them if you find any damage or wear. A timely replacement prevents bigger issues and ensures the machine runs smoothly.
Sourcing Replacements
Finding the right parts for your Taylor Ice Cream Machine is crucial. Use genuine Taylor parts for the best performance and longevity. Follow these steps to source replacements:
- Visit the Taylor official website.
- Navigate to the parts section.
- Search for the specific part number.
- Add the part to your cart and proceed to checkout.
Alternatively, contact your local Taylor service provider. They can guide you on the correct parts for your model. Always verify the part compatibility before purchase.
Part | Signs of Wear | Action |
---|---|---|
Seals | Cracks, leaks | Replace |
O-rings | Wear, tear | Replace |
Gaskets | Damage, deformation | Replace |
Blades | Dullness, chipping | Replace |
By sourcing and replacing worn parts promptly, you ensure your Taylor Ice Cream Machine operates efficiently. This proactive maintenance helps deliver the perfect ice cream every time.

Credit: www.taylorwi.net
Professional Help
Maintaining a Taylor Ice Cream Machine is important for smooth operation. Sometimes, problems arise that need more than basic troubleshooting. In these cases, seeking professional help ensures your machine returns to optimal performance quickly.
When To Call A Technician
Some issues require expert intervention. If you notice consistent machine errors, strange noises, or poor ice cream quality, it’s time to call a technician. Also, if your machine frequently trips electrical circuits, don’t attempt repairs yourself. Technicians have the tools and knowledge to handle these problems safely.
Issue | When to Call a Technician |
---|---|
Machine Errors | Consistent error messages on the display. |
Strange Noises | Unusual sounds coming from the machine. |
Poor Quality | Soft or runny ice cream. |
Electrical Issues | Machine trips electrical circuits often. |
Choosing A Service Provider
Choosing the right service provider ensures your Taylor Ice Cream Machine gets the best care. Here are some tips:
- Check Credentials: Ensure the technician is certified to work on Taylor machines.
- Read Reviews: Look at customer reviews for insight into their service quality.
- Experience: Choose providers with years of experience in ice cream machine repair.
- Warranty: Ensure they offer a warranty on their repair work.
By following these tips, you can trust your machine is in good hands.
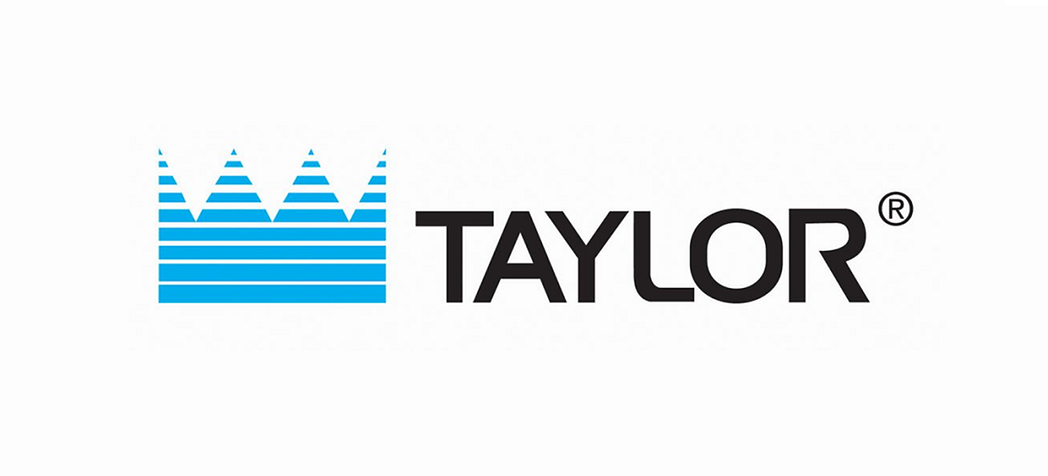
Credit: www.partstown.com
Frequently Asked Questions
Why Is My Ice Cream Machine Not Dispensing Ice Cream?
Your ice cream machine might not dispense due to a clogged nozzle, low mix levels, or motor issues. Check and clean the nozzle, refill the mix, and ensure the motor functions properly. Regular maintenance helps prevent problems.
Why Is My Ice Cream Machine Not Freezing?
Your ice cream machine may not freeze due to low refrigerant levels, a faulty compressor, or incorrect temperature settings. Check for blockages in the cooling vents and ensure proper ventilation.
How Do You Reset Beater Overload Taylor?
To reset the beater overload on a Taylor machine, press the reset button located on the control panel. Ensure the machine is off before resetting.
How Do You Fix The Freezer Lock On A Taylor Ice Cream Machine?
To fix the freezer lock on a Taylor ice cream machine, ensure the machine is off. Inspect the lock mechanism for obstructions. Clean and lubricate the lock. Replace any damaged parts if necessary. If issues persist, consult the user manual or contact Taylor customer support.
Conclusion
Troubleshooting a Taylor ice cream machine can be straightforward with the right guidance. Regular maintenance helps prevent common issues. Always consult the manual for specific problems. Reach out to professionals if needed. Your ice cream machine will run smoothly, ensuring delicious treats every time.
Keep these tips handy for future reference.