Ensure your Porter Cable air compressor is plugged in and the power switch is on. Check for any tripped breakers or blown fuses.
Porter Cable air compressors are reliable tools, but they may occasionally require troubleshooting. Identifying and resolving common issues can help maintain optimal performance. Check for proper electrical connections and ensure there are no tripped breakers or blown fuses. Inspect the air hoses and fittings for leaks or damage.
Regular maintenance, such as cleaning or replacing filters, can prevent many problems. If the compressor fails to start, examine the pressure switch and motor for faults. Understanding these basic troubleshooting steps can save time and extend the life of your Porter Cable air compressor.
Common Issues
Porter Cable air compressors are popular for their reliability and efficiency. But, like any other machine, they can experience problems. In this section, we discuss common issues you might face.
Air Leaks
Air leaks are a frequent issue with air compressors. They can reduce efficiency and waste energy.
- Check hoses: Inspect all hoses for wear and tear.
- Tighten fittings: Ensure all fittings are snug and secure.
- Use soapy water: Spray soapy water to find leaks. Bubbles will appear at leak points.
Addressing air leaks promptly can save you money and improve performance.
Motor Won’t Start
A non-starting motor can be frustrating. Several factors can cause this issue.
- Check the power source: Ensure the compressor is plugged in and switched on.
- Inspect the pressure switch: If faulty, it may prevent the motor from starting.
- Examine the capacitor: A failing capacitor can hinder the motor.
Use a multimeter to check electrical components. Replace any faulty parts to get your compressor running again.

Credit: www.amazon.com
Tools Needed
To troubleshoot your Porter Cable air compressor efficiently, you need the right tools. Using the correct tools ensures safety and precision. Below, we outline the essential tools required.
Basic Toolkit
A basic toolkit is indispensable for troubleshooting. Here are some must-have items:
- Screwdrivers: Both flat-head and Phillips screwdrivers are necessary.
- Wrenches: Adjustable and socket wrenches help loosen tight bolts.
- Pliers: Needle-nose and slip-joint pliers for gripping and cutting.
- Allen Wrenches: These are essential for hexagonal bolts.
- Hammer: A small hammer can be useful for tapping parts.
Specialized Tools
Specialized tools can make troubleshooting more effective. Below are some specialized tools you may need:
- Multimeter: For checking electrical circuits and components.
- Pressure Gauge: To measure air pressure accurately.
- Leak Detection Spray: Identifies air leaks quickly and easily.
- Oil Extractor: Helps in changing compressor oil efficiently.
- Air Compressor Oil: Ensure you have the correct type for your model.
Using these tools will make troubleshooting your Porter Cable air compressor straightforward. Having them at hand ensures you can address issues quickly and safely.
Safety Precautions
Troubleshooting a Porter Cable air compressor can be risky. Follow these safety precautions to protect yourself from harm. Always prioritize safety to prevent accidents.
Personal Protective Equipment
Always wear the right personal protective equipment (PPE) when working with air compressors. Use the following items to stay safe:
- Safety glasses to protect your eyes from debris.
- Gloves to shield your hands from cuts and chemicals.
- Ear protection to guard against loud noise.
- Steel-toe boots to protect your feet from heavy objects.
Safe Handling
Handling an air compressor safely is crucial. Follow these steps for safe operation:
- Ensure the air compressor is on a stable surface.
- Check the power cord for any damage before use.
- Keep the area around the compressor clear of obstacles.
- Always turn off the compressor before performing maintenance.
- Release the air pressure from the tank before troubleshooting.
Refer to the table below for a quick safety checklist:
Safety Measure | Action |
---|---|
Wear PPE | Glasses, gloves, ear protection, boots |
Stable Surface | Ensure the compressor is steady |
Check Power Cord | Inspect for any damage |
Clear Area | Remove obstacles around the compressor |
Turn Off Compressor | Before maintenance, ensure it’s off |
Release Pressure | Before troubleshooting, release air pressure |
Air Leaks Solutions
Air leaks in your Porter Cable Air Compressor can cause major problems. These leaks reduce efficiency and can lead to more serious issues. Fixing air leaks improves performance and extends the life of your compressor.
Identifying Leaks
To identify leaks, listen for hissing sounds. Use a soapy water solution on connections. Bubbles indicate a leak. Check around hoses, fittings, and the tank.
Component | Common Leak Signs |
---|---|
Hoses | Visible cracks or worn areas |
Fittings | Bubbles when tested with soapy water |
Tank | Corrosion or rust spots |
Fixing Leaks
Fixing leaks is simple with the right tools. Use Teflon tape on threaded fittings. Replace damaged hoses with new ones. Tighten loose connections using a wrench.
- Turn off the compressor and release air pressure.
- Wrap Teflon tape around threaded fittings.
- Replace any damaged or cracked hoses.
- Tighten all loose connections with a wrench.
After fixing, retest with soapy water to ensure no bubbles. Make sure your compressor is leak-free and ready for use.
Motor Issues
Is your Porter Cable air compressor not working? Motor issues are common. This guide covers electrical and mechanical problems. Understand the issues and fix them easily.
Electrical Problems
Electrical problems can often stop the motor. Check the power supply first. Ensure that the compressor is plugged in. Also, check the circuit breaker. It might have tripped.
Inspect the power cord for damages. Look for cuts or burns. Replace the cord if damaged. Next, check the on/off switch. Use a multimeter to test it. Replace the switch if faulty.
Examine the motor capacitor. A bad capacitor can prevent the motor from starting. Use a multimeter to check its health. Replace the capacitor if it is bad.
Mechanical Failures
Mechanical failures can also cause motor issues. First, check the belt if your model has one. A loose or broken belt stops the motor. Tighten or replace the belt as needed.
Inspect the motor bearings. Worn-out bearings can cause noise or motor failure. Lubricate the bearings if needed. If they are too worn, replace them.
Look at the piston and cylinder. Dirt or debris can cause problems. Clean these parts regularly. Ensure that the piston moves freely.
Issue | Possible Cause | Solution |
---|---|---|
Motor not starting | Power supply issue | Check power cord and switch |
Motor noisy | Worn bearings | Lubricate or replace bearings |
Motor overheating | Dirty piston | Clean piston and cylinder |

Credit: www.manua.ls
Pressure Problems
Pressure problems in a Porter Cable air compressor can affect its performance. Understanding the common issues can help you fix them quickly. Let’s discuss two main pressure problems: Low Pressure and Over-Pressurization.
Low Pressure
Low pressure can slow down your work. This issue can have several causes:
- Clogged air filter
- Leaking hoses or fittings
- Faulty pressure switch
First, check the air filter. A dirty filter can restrict air flow. Clean or replace it if needed. Next, inspect the hoses and fittings. Look for air leaks and seal them with tape.
The pressure switch could also be the problem. Use a multimeter to test it. If it’s faulty, replace it.
Over-pressurization
Over-pressurization can be dangerous. It can damage the compressor. Possible reasons include:
- Malfunctioning pressure relief valve
- Defective pressure switch
First, check the pressure relief valve. This valve prevents excess pressure. Test and replace it if needed. Next, inspect the pressure switch. A faulty switch can cause over-pressurization. Use a multimeter to check it. Replace it if necessary.
Here is a summary table for quick reference:
Issue | Possible Causes | Solutions |
---|---|---|
Low Pressure |
|
|
Over-Pressurization |
|
|
Maintenance Tips
Proper maintenance ensures your Porter Cable air compressor works efficiently. Regular care prevents breakdowns and extends the life of your compressor. Follow these maintenance tips to keep your air compressor in top shape.
Regular Inspections
Performing regular inspections helps identify issues early. Check for any visible damage or leaks. Inspect the hoses and fittings for wear and tear.
- Check oil levels and refill if necessary.
- Ensure the air filter is clean.
- Inspect the pressure switch for proper operation.
Cleaning And Lubrication
Cleaning and lubrication are essential for smooth operation. Dirt and debris can damage the compressor.
Component | Cleaning Frequency | Lubrication Frequency |
---|---|---|
Air Filter | Monthly | Not Applicable |
Oil Reservoir | Check Monthly | Every 3 Months |
Hoses | Weekly | Not Applicable |
- Turn off and unplug the compressor before cleaning.
- Remove dirt from the air filter with a soft brush.
- Refill the oil reservoir if the level is low.
Following these tips ensures your Porter Cable air compressor runs efficiently. Regular maintenance saves money and prevents unexpected breakdowns.
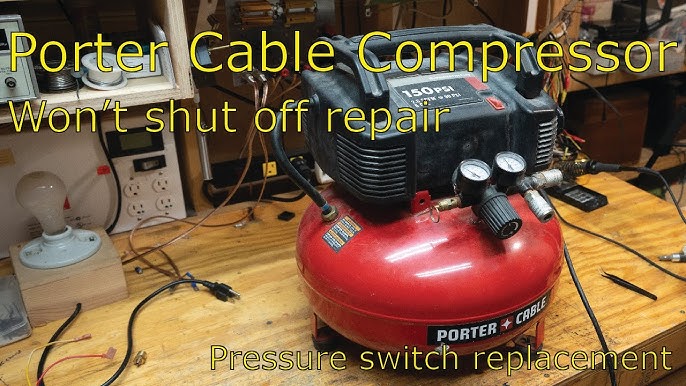
Credit: m.youtube.com
When To Call A Professional
Troubleshooting a Porter Cable Air Compressor can sometimes be straightforward. But there are moments when professional help is needed. Knowing when to call a professional can save you time and money.
Complex Repairs
Some repairs are too complex for DIY fixes. Electrical issues or motor problems fall into this category. These issues often require specialized tools and expertise.
Attempting to fix these without proper knowledge can be dangerous. It could also void the warranty or cause further damage.
Here are some signs that you need professional help:
- Strange noises from the compressor
- Frequent overheating
- Electrical sparks or smoke
Warranty Concerns
Your air compressor may still be under warranty. If so, any DIY repairs might void it. Check your warranty terms before attempting any fixes.
Here’s a quick guide on what to check:
Warranty Aspect | Details |
---|---|
Duration | Typically 1-3 years |
Coverage | Parts and labor |
Conditions | Use only authorized service centers |
Authorized service centers know how to handle warranty repairs. They ensure your compressor is fixed correctly and keeps the warranty intact.
In summary, call a professional for complex repairs or warranty concerns. This ensures your Porter Cable Air Compressor remains in top condition.
Frequently Asked Questions
Why Is The Air Compressor Not Building Up Pressure?
The air compressor may not build pressure due to leaks, faulty valves, or a damaged pressure switch. Check for air leaks, inspect valves, and ensure the pressure switch works correctly. Regular maintenance helps prevent these issues.
How To Troubleshoot An Air Compressor?
Check power supply and connections. Inspect for leaks, unusual noises, and vibrations. Clean or replace air filters. Examine and tighten belts. Consult the manual for error codes.
Why Did My Electric Air Compressor Stop Working?
Your electric air compressor might have stopped working due to a tripped circuit breaker, blown fuse, or motor issues. Check for overheating or insufficient power supply. Inspect the pressure switch and safety valve for faults. Ensure proper maintenance and clean filters regularly.
Why Is My Air Compressor Cutting Out?
Your air compressor may cut out due to overheating, low oil levels, or an overloaded circuit. Check for blockages and ensure proper ventilation. Regular maintenance helps prevent these issues.
Conclusion
Solving issues with your Porter Cable air compressor can be straightforward with the right guidance. Regular maintenance ensures optimal performance and longevity. Follow these troubleshooting tips to keep your equipment running smoothly. Always refer to the user manual for specific instructions.
A well-maintained compressor saves time and money in the long run.