To troubleshoot a Follett ice machine, start by checking the power supply and ensuring the machine is turned on. Clean the condenser coils regularly to maintain efficiency.
Follett ice machines are known for their reliability and efficiency. Despite their high quality, issues can arise that require troubleshooting. Proper maintenance and timely interventions can prevent common problems. Start by checking the basics: ensure the machine is plugged in and the power is on.
Clean the condenser coils to avoid overheating and inefficiency. Regularly inspect for any signs of wear or damage. Addressing these issues promptly can extend the life of your ice machine. Always refer to the user manual for specific guidance. Keeping your Follett ice machine in top condition ensures a steady supply of ice for your needs.
Common Issues
Follett ice machines are reliable, but sometimes they face problems. Knowing the common issues helps you troubleshoot quickly.
Machine Not Turning On
If your Follett ice machine is not turning on, check these points:
- Power Supply: Ensure the machine is plugged in correctly.
- Fuse: Check if the fuse is blown and replace it if needed.
- Power Switch: Make sure the power switch is in the “on” position.
These are the first steps to diagnose power issues.
Ice Not Forming
Sometimes the machine runs but doesn’t make ice. Here are some checks:
- Water Supply: Ensure the water supply is connected and open.
- Water Filter: Check if the filter is clogged and clean it.
- Temperature: Ensure the ambient temperature is within the machine’s operating range.
If these steps don’t help, you may need a technician.
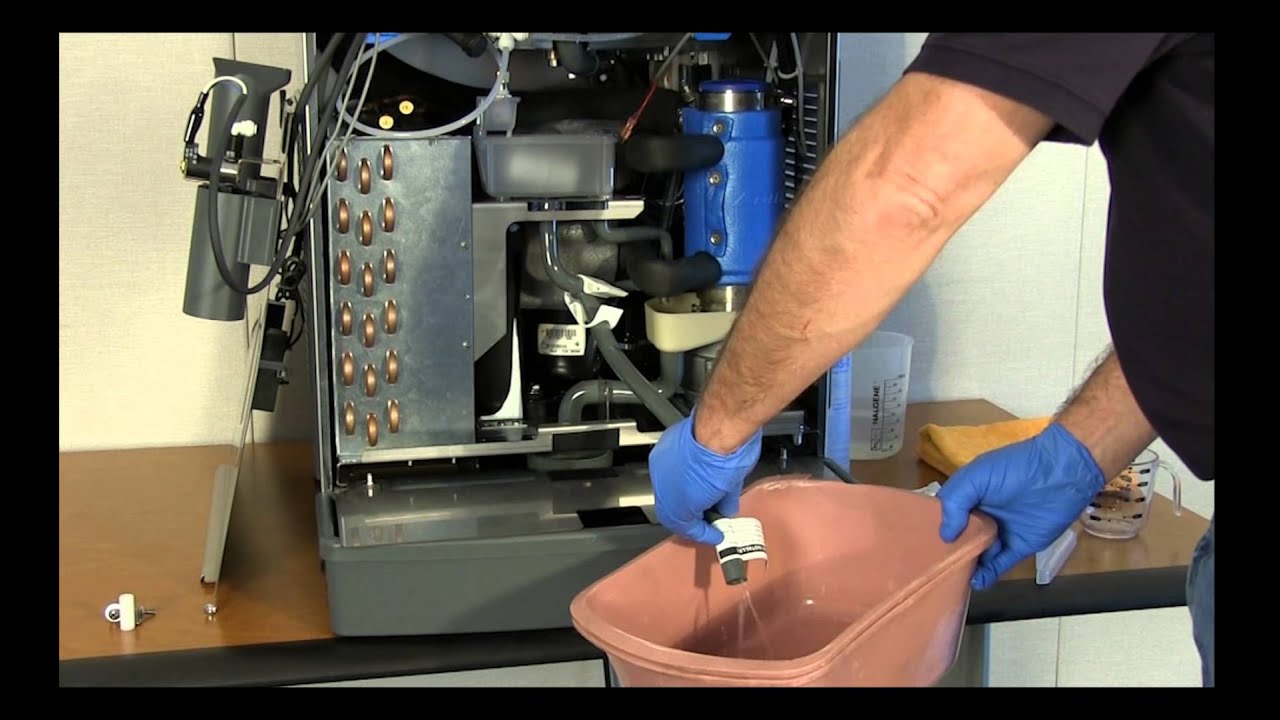
Credit: m.youtube.com
Pre-troubleshooting Checks
Before diving into troubleshooting your Follett ice machine, perform some basic checks. These initial steps can save time and effort. They help identify simple issues quickly. Let’s start with the essentials.
Power Supply
First, check the power supply. Ensure the machine is plugged in securely. Verify that the outlet is working. Use another device to check the outlet. If the outlet is faulty, change it or call an electrician.
Inspect the power cord for damage. Replace it if necessary. Check the circuit breaker. Reset it if it has tripped. A stable power supply is crucial for the ice machine’s operation.
Water Connection
Next, check the water connection. Ensure the water supply valve is open. Verify that the water line is not kinked or blocked. A steady water flow is essential for making ice.
Inspect the water filter. Replace it if it is clogged. Clean the water inlet valve. A clean valve ensures a smooth water supply. Consistent water flow is key for optimal ice production.
Check | Action |
---|---|
Power Supply |
|
Water Connection |
|
Diagnosing Electrical Problems
Troubleshooting electrical problems in a Follett ice machine can be challenging. Understanding electrical issues is crucial for proper maintenance. This section will guide you through key steps in diagnosing electrical problems.
Fuse Inspection
Fuses protect your ice machine from electrical surges. A blown fuse can stop the machine from working. Inspecting fuses is a simple process.
- First, turn off the ice machine.
- Locate the fuse box. This is usually near the power cord.
- Open the fuse box using a screwdriver.
- Look for any burnt or broken fuses. Replace them if necessary.
Use a multimeter to test the fuse’s continuity. If there is no continuity, the fuse is blown. Replace it with a new fuse of the same rating.
Circuit Breaker
A tripped circuit breaker can also halt your ice machine. Checking the circuit breaker is another essential step.
- Locate the circuit breaker panel. It is usually near the main power supply.
- Identify the breaker for your ice machine. It should be labeled.
- If the breaker is tripped, it will be in the middle position. Flip it to the “Off” position, then back to the “On” position.
If the breaker trips again, there could be a short circuit or other electrical issues. In this case, consult a professional technician.
Problem | Solution |
---|---|
Blown Fuse | Replace with same rating fuse |
Tripped Breaker | Reset the breaker |
Regular inspection of fuses and circuit breakers can keep your Follett ice machine running smoothly. Proper electrical maintenance ensures the longevity of your machine.
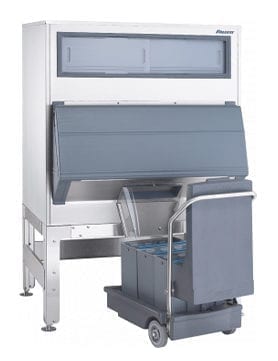
Credit: www.easyice.com
Addressing Water Flow Issues
Experiencing water flow issues with your Follett ice machine can be frustrating. To keep your ice machine running smoothly, it’s essential to address these problems promptly. Below are common causes and solutions for water flow issues.
Clogged Filters
Clogged filters can significantly impact the water flow in your Follett ice machine. Over time, filters accumulate debris and mineral deposits, restricting the water flow.
- Inspect the filter: Remove and inspect the filter for any visible blockages.
- Clean or replace: If the filter is dirty, clean it with a soft brush. If it’s heavily clogged, consider replacing it.
- Regular maintenance: Establish a routine to check and clean the filters regularly to prevent future blockages.
Blocked Valves
Blocked valves can also cause water flow issues. These valves control the water entering the machine. When they are blocked, water cannot flow freely.
Step | Description |
---|---|
1 | Turn off the machine: Ensure the machine is powered off before inspecting the valves. |
2 | Locate the valve: Find the valve that controls the water flow into the machine. |
3 | Check for blockages: Inspect the valve for any obstructions or debris. |
4 | Clear the blockage: Use a small brush or tool to gently remove any debris. |
Keeping your Follett ice machine free from water flow issues ensures it operates efficiently. Regular maintenance and timely troubleshooting can save you time and money in the long run.
Temperature Control
Proper temperature control is crucial for a Follett Ice Machine. If the temperature is off, the machine might not produce ice efficiently. Understanding how to adjust and monitor the temperature ensures optimal performance.
Thermostat Settings
The thermostat in your Follett Ice Machine regulates the internal temperature. Check the thermostat settings to ensure they match the recommended levels.
- Set the thermostat to the manufacturer’s suggested temperature.
- Check the thermostat regularly for accuracy.
- Adjust as needed to maintain a stable temperature.
A malfunctioning thermostat can lead to inconsistent ice production. Verify that the thermostat is working correctly to avoid issues.
Ambient Temperature
The ambient temperature around the ice machine affects its performance. Keep the machine in an area with a stable temperature.
Condition | Recommended Temperature |
---|---|
Operating Room | 70-75°F (21-24°C) |
Storage Room | 65-70°F (18-21°C) |
High ambient temperatures can cause the machine to overwork. Ensure proper ventilation around the ice machine to maintain a cool environment.
Use fans or air conditioners if the room temperature is too high. This helps in maintaining the ambient temperature within the recommended range.
Cleaning And Maintenance
Regular cleaning and maintenance of your Follett ice machine ensures longevity and efficiency. Proper care prevents breakdowns and ensures safe, clean ice production. Below, we discuss the descaling process and sanitizing components to keep your machine in top shape.
Descaling Process
Descaling removes mineral buildup in your Follett ice machine. Follow these steps:
- Turn off and unplug the ice machine.
- Remove all ice from the storage bin.
- Prepare a descaling solution per the manufacturer’s guidelines.
- Pour the solution into the water reservoir.
- Run a cleaning cycle to circulate the solution.
- Drain the solution and rinse the machine with fresh water.
- Repeat the rinse cycle to ensure no descaling solution remains.
Descaling should be done every six months to prevent mineral buildup.
Sanitizing Components
Sanitizing ensures your ice remains free from contaminants. Follow these steps:
- Turn off the ice machine and unplug it.
- Remove all detachable components like the ice bin and water tray.
- Prepare a sanitizing solution as per the instructions.
- Soak the components in the solution for at least 10 minutes.
- Rinse the components thoroughly with clean water.
- Wipe down the interior surfaces with a clean, damp cloth.
- Allow all components to air dry before reassembling.
Sanitizing should be performed monthly to maintain hygiene.
Following these cleaning and maintenance steps ensures your Follett ice machine functions efficiently and produces safe, clean ice. Consistent care reduces the need for costly repairs and extends the machine’s lifespan.
When To Call A Professional
Follett ice machines are robust and reliable. Yet, sometimes they need professional intervention. Identifying when to call a professional can save you time and money.
Complex Electrical Issues
Electrical issues can be dangerous. If your ice machine has electrical problems, it’s time to call a professional. These issues can include:
- Frequent tripping of circuit breakers
- Burning smells or smoke
- Ice machine not powering on
Electrical repairs need special tools and knowledge. Don’t risk your safety or the machine’s functionality.
Major Mechanical Failures
Mechanical parts can break or wear out. Major mechanical failures often need professional repair. These failures might include:
- Broken compressor
- Malfunctioning fans
- Severe leaks
Attempting these repairs yourself can lead to more damage. Professionals have the skills to fix these issues correctly.
Issue | When to Call a Professional |
---|---|
Electrical problems | Frequent circuit breaker trips, burning smells |
Mechanical failures | Broken compressor, malfunctioning fans |
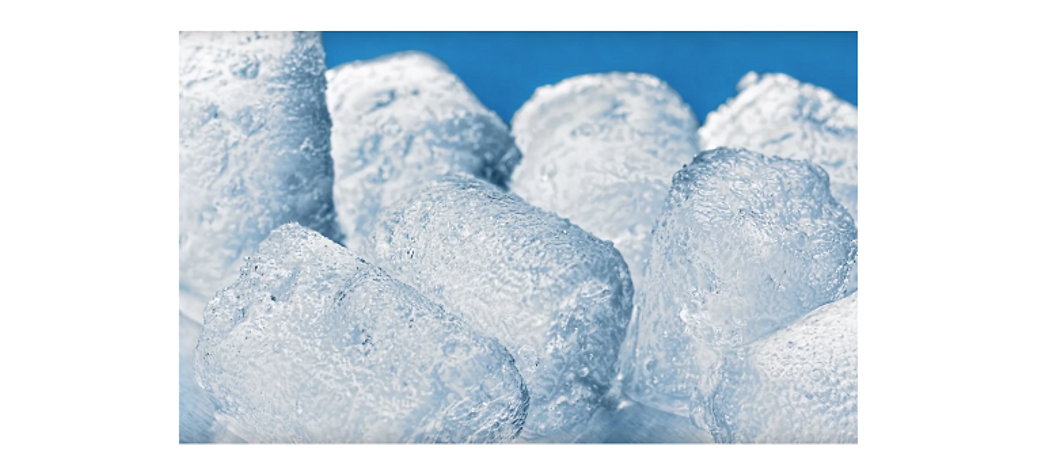
Credit: www.partstown.com
Preventive Measures
Preventive measures help keep your Follett ice machine running smoothly. Taking care of the machine ensures it lasts longer and works efficiently. Let’s explore some key preventive actions.
Regular Inspections
Regular inspections are essential for maintaining your Follett ice machine. Schedule monthly checks to spot any potential issues early. Look for signs of wear and tear on key parts.
Check the ice bin for cleanliness. A dirty ice bin can affect the quality of ice. Make sure the water supply is clean and free from contaminants. Inspect the electrical connections for any signs of damage or loose wires.
Inspection Item | Frequency |
---|---|
Ice Bin Cleanliness | Monthly |
Water Supply Check | Monthly |
Electrical Connections | Monthly |
Scheduled Servicing
Scheduled servicing keeps your Follett ice machine in top condition. Hire a professional technician for thorough servicing. This should be done every six months.
The technician will clean all parts and replace worn components. They will also check the refrigerant levels and adjust settings for optimal performance. Document every service to track the machine’s maintenance history.
- Clean all parts
- Replace worn components
- Check refrigerant levels
- Adjust settings
Following these preventive measures ensures your Follett ice machine runs efficiently. Regular care helps avoid costly repairs and downtime. Keep your ice machine in excellent condition with routine inspections and servicing.
Frequently Asked Questions
Why Isn’t My Follett Ice Machine Making Ice?
Your Follett ice machine might not make ice due to power issues, clogged filters, or faulty components. Check the water supply, clean the filters, and ensure the machine has power. If problems persist, consult the user manual or contact customer support.
How Do I Reset A Follett Ice Machine?
To reset a Follett ice machine, turn off the power, wait 10 seconds, then turn it back on. Check the user manual for specific instructions.
Why Is My Ice Maker Not Making Ice But Water Works?
Your ice maker might not make ice due to a clogged filter, faulty water inlet valve, or a malfunctioning thermostat.
Why Is My Portable Ice Maker Not Making Ice?
Your portable ice maker may not be making ice due to power issues, low water levels, or a clogged water line. Ensure it’s plugged in, has enough water, and check for obstructions. Clean the machine regularly to maintain optimal performance.
Conclusion
Troubleshooting your Follett ice machine can be straightforward with the right tips. Regular maintenance prevents common issues. Follow the steps outlined to ensure efficient operation. Keeping your machine in top shape ensures a steady supply of ice. For persistent problems, contact a professional technician.
With proper care, your Follett ice machine will serve you well.