Hexgaming and Scuf offer high-end custom PS5 controllers, but they differ in customization options and price points. Both prioritize enhancing gameplay with ergonomic designs and customizable features.
Gamers seeking to elevate their PlayStation 5 experience often find themselves comparing Hexgaming and Scuf controllers. These brands stand out in the market for their commitment to improving precision, comfort, and overall gaming performance. Hexgaming controllers boast extensive customization choices, from button mapping to cosmetic alterations, allowing for a highly personalized gaming experience.
Scuf controllers, on the other hand, offer a rich history of quality with patented paddle control systems and interchangeable parts designed for the competitive player. Each brand has cultivated a loyal following by catering to both the casual gamer desiring more comfort and the professional looking for that competitive edge. As gaming evolves, these controllers continue to set the standard for what gamers expect from their hardware.

Credit: www.amazon.sg
Introduction To Hexgaming And Scuf
Hexgaming and Scuf are big names in gaming peripherals. They create custom controllers for gamers. Their PS5 controllers are very popular. Players love them for their style and performance. Both brands are all about giving you the edge in gaming.
High Stakes In Gaming Peripherals
The gaming world is always growing. Gamers want the best gear. Hexgaming and Scuf controllers are top choices. Players need speed, comfort, and precision. These brands deliver all of those.
Evolving Needs Of Gamers
Gamers’ needs are changing fast. They want more than just standard controllers. Hexgaming and Scuf offer custom features. These include remappable buttons and ergonomic designs. Gamers can play longer and better with these controllers.
Design And Aesthetics
The ultimate controller can transform a gaming session into an immersive experience. In the realm of performance gaming, Hexgaming and Scuf controllers stand out. Both brands boast high-quality features, yet their design and aesthetics cater to different tastes and preferences. Let’s delve deeper and compare how Hexgaming and Scuf PS5 controllers stack up in terms of ergonomics, customization, and personalization.
Ergonomic Considerations
Comfort plays a huge role in controller design. Hexgaming and Scuf both prioritize a design that fits well in players’ hands. These controllers aim to minimize hand fatigue during extended gaming sessions. Let’s compare their ergonomic features:
- Hexgaming controllers feature a customizable grip texture.
- Scuf controllers are known for their signature paddles and ergonomic shape.
Both controllers have adjustable triggers and thumbsticks that enhance the gaming experience.
Customization And Personalization
Personalization makes a controller more than just a tool; it becomes an extension of the gamer. Hexgaming and Scuf take personalization seriously, offering a range of options:
Feature | Hexgaming | Scuf |
---|---|---|
Customizable Shell Colors | Yes | Yes |
Customizable Thumbsticks | Multiple Options | Limited Options |
Customizable Buttons | Yes | Yes |
Engravings | Yes | No |
Hexgaming takes the lead in customization with exclusive shell patterns and the option for engravings.
Performance And Responsiveness
For gamers, performance and responsiveness are the keys to victory. Choosing between Hexgaming and Scuf PS5 controllers? Let’s dive deep into what sets them apart. Both brands promise an enhanced gaming experience, but details matter when milliseconds can lead to triumph or defeat.
Button Layout And Accessibility
Customizable button layouts set Hexgaming and Scuf apart. These elite controllers adapt to your hands. Their aim is simple: never miss a beat in high-stress gaming.
- Hexgaming’s controllers boast remappable rear buttons. This means quick access to critical actions.
- Scuf controllers also offer similar features with their signature paddle controls. Players find improved reaction times.
Trigger Mechanisms And Thumbsticks
Sensitivity in triggers and thumbsticks proves crucial. Both brands have solutions. Hexgaming features rapid-fire triggers. Scuf showcases adjustable triggers. Both minimize motion. This saves precious time.
Trigger/Thumbstick Feature | Hexgaming | Scuf |
---|---|---|
Rapid-Fire Triggers | Yes | No |
Adjustable Triggers | No | Yes |
Interchangeable Thumbsticks | Yes | Yes |
Both Hexgaming and Scuf offer interchangeable thumbsticks. This caters to different grip styles and hand sizes. Enhanced grip patterns prevent slips during intense gameplay. Both raise the bar for precision and control.
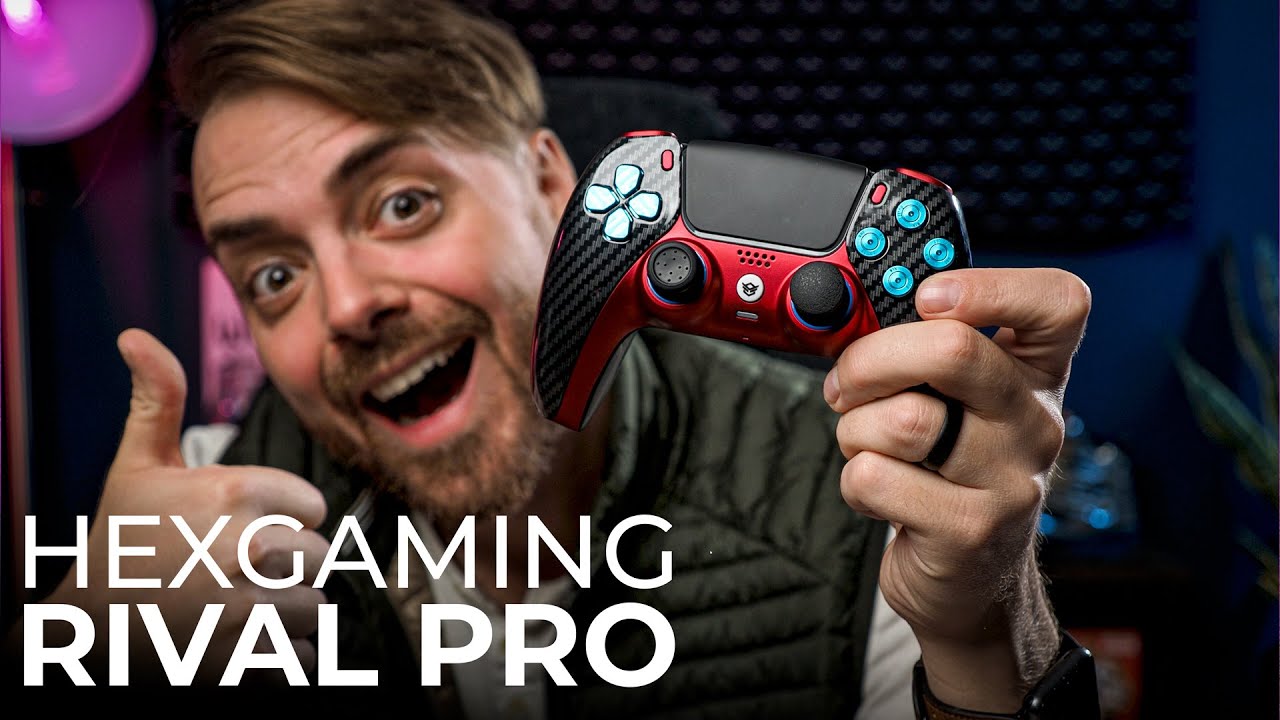
Credit: m.youtube.com
Durability And Build Quality
When talking about high-end gaming controllers, the user experience is not just about performance. Durability and build quality play a huge part in the longevity and feel of the controller. Both Hexgaming and Scuf have established reputations in the gaming world, but how do they stack up when it comes to withstanding the test of time and extensive gaming sessions? Let’s dive into the materials and craftsmanship, followed by warranty and support for each brand.
Materials And Craftsmanship
Quality materials are the backbone of any durable product. Hexgaming controllers boast a robust structure. They use top-quality plastics and metals for buttons and triggers. The grip areas are designed with anti-slip textures, ensuring a solid hold during intense gaming sessions. Scuf controllers also prioritize durability with sturdy materials. Their key innovation lies in their patented paddle control system adding to the overall build integrity.
- Hexgaming: Anti-slip grip, metallic accents.
- Scuf: Patented paddle system, high-quality plastics.
Warranty And Support
Warranty policies are a telling sign of a company’s confidence in their product. Hexgaming offers a 6-month warranty that covers any manufacturing defects. Their customer support is reachable for queries and issues, promising a quick turnaround for concerns. Scuf, on the other hand, provides a similar 6-month warranty period, with a supportive team to help gamers through any issue. They ensure that gamers can get back to their favorite titles with minimal downtime.
Brand | Warranty Period | Support Quality |
---|---|---|
Hexgaming | 6 Months | Responsive and Helpful |
Scuf | 6 Months | Efficient and User-Friendly |
Choosing between Hexgaming and Scuf PS5 controllers boils down to personal preference in design and minor differences in materials and ergonomics. Both brands provide solid options that stand the test of time. Now, it’s up to you to decide which controller’s build quality aligns with your gaming style and preferences.
Compatibility And Connectivity
When choosing a PS5 controller, two names often come up: HexGaming and Scuf. Both controllers bring excitement to gaming with unique features. But, it is vital to check how they work with PS5 consoles. This section will look into their compatibility and connectivity.
Console Integration
Gamers want seamless play with their PS5 consoles. We analyze if HexGaming and Scuf controllers offer this. HexGaming controllers match perfectly with the PS5, allowing full use of all console features. They support all PS5 games and easily sync with the system.
Scuf controllers also boast excellent integration. They offer wireless playing for a cord-free experience. Their compatibility with the PS5’s features ensures a top-notch gaming adventure. Let’s dig deeper into how they maintain this integration through updates.
Software And Firmware Updates
Staying up-to-date is critical for peak performance. Both HexGaming and Scuf controllers get regular updates.
- HexGaming automatically receives updates when connected to a PS5. No extra steps are needed.
- Scuf controllers need manual updates via a PC. It is an easy process that ensures optimal functionality with the PS5.
By regularly updating, these controllers maintain compatibility with the latest PS5 games and features. They also improve their performance and iron out any issues faced during gameplay. Excellent connectivity is vital for controller performance, and both brands take it seriously.
Price Comparison
Entering the world of gaming with the right controller is crucial. PS5 owners face a big decision: Hexgaming or Scuf controllers. Price matters in this high-stakes game. Let’s break down what each brand offers for the price tag.
Cost-Benefit AnalysisCost-benefit Analysis
Hexgaming and Scuf controllers both boast advanced features. They’re not your average gamepads.
Use of table to compare prices
Brand | Base Price | Custom Options | Total Cost |
---|---|---|---|
Hexgaming | $189 | Up to $50 | $239 |
Scuf | $169 | Up to $40 | $209 |
Investing more in Hexgaming could yield unique customizations. Scuf’s lower base price offers a gentler start. Reflect on the features essential for your gameplay.
Investment for Competitive GamersInvestment For Competitive Gamers
Competitive gamers eye the long-term benefits a controller can offer. It’s an investment.
- Better performance: Enhanced accuracy and speed.
- Comfort: Extended play with less fatigue.
- Customization: Tailored to your gaming style.
Both brands aim high in competitive circles. Hexgaming’s higher cost echoes its bespoke customization. Scuf’s pricing aligns with accessibility and performance. Choose based on your professional gaming trajectory.
User Reviews And Community Feedback
Hexgaming and Scuf are big names in the gaming world. They both make controllers for the PS5. Many gamers talk about them online. They share thoughts on how good these controllers are. Let’s dive into what people are saying.
Pros And Cons From Consumer Perspective
Gamers like and dislike different things about these controllers.
Hexgaming Controllers | Scuf Controllers |
---|---|
|
|
Expert Opinions And Endorsements
Experts in gaming also have thoughts on these controllers.
- Comfort: Scuf wins for long gaming.
- Customization: Hexgaming offers more choices.
- Price: Both are seen as investments in gaming.
Famous gamers use these brands, too. This could mean they trust these controllers a lot.

Credit: www.gamepitt.co.uk
Final Verdict
When gamers face the tough decision of choosing a PS5 controller, two names stand out: Hexgaming and Scuf. Both brands offer advanced features, aiming to enhance the gaming experience. Let’s dive into which controller might claim the top spot for eager gamers ready to level up.
Choosing The Right Controller
Customization and comfort dictate the gaming journey. Hexgaming controllers boast personalized touchpads and interchangeable thumbsticks. Scuf controllers counter with ergonomic designs and adjustable triggers. Gamers must weigh these attributes to pick their perfect ally.
- Hexgaming: Offers extensive customization.
- Scuf: Prioritizes a comfortable grip.
Future Of Ps5 Controllers
The future shines bright for PS5 controllers. Advances lean towards adaptive triggers and haptic feedback. Both Hexgaming and Scuf seem ready. They already integrate these features, promising gamers a more immersive experience as technology evolves.
- Immersive Technology: Enhanced gameplay with new features.
- Adaptability: Controllers that grow with future games.
Frequently Asked Questions Of Hexgaming Vs Scuf Ps5 Controllers
Is Hexgaming Ps5 Controller Any Good?
The HexGaming PS5 controller is well-regarded for its customization options and pro gaming features, making it a solid choice for serious gamers.
Is The Ps5 Scuf Controller Worth It?
The PS5 SCUF controller is worth considering for gamers valuing customization options, ergonomic designs, and performance features. Its higher price reflects the advanced controls and potential competitive edge it provides.
What Is The Best Ps5 Controller In The World?
The best PS5 controller is widely considered to be the DualSense Wireless Controller, known for its haptic feedback and adaptive triggers.
Is A Scuf Controller Better Than A Regular Controller?
A SCUF controller offers enhanced customization and ergonomic features over a regular controller, potentially improving gaming performance.
Conclusion
Deciding between Hexgaming and Scuf PS5 controllers boils down to personal preference and playstyle. Both offer enhanced gaming experiences with custom features and superior ergonomics. Remember to weigh your options based on functionality, comfort, and budget. Whichever you choose, you’re leveling up your game.
Embrace the upgrade and dominate the competition.