Check the boiler’s power supply and ensure the thermostat is set correctly. Inspect for error codes on the display.
Laars boilers are known for their reliability and efficiency, but occasional issues can arise. Common problems include power supply interruptions, thermostat settings, or error codes that indicate specific faults. Regular maintenance and timely troubleshooting can keep your Laars boiler running smoothly.
Understanding the basics of troubleshooting can save time and money. Ensure you check the power connections, thermostat settings, and error codes first. These steps often resolve most issues quickly. If problems persist, consulting the user manual or contacting a professional can provide further guidance. Proper care and attention help extend the lifespan of your Laars boiler.
Common Issues
Laars boilers are reliable and efficient. But sometimes, issues arise. Troubleshooting these common issues can help maintain a warm home. Below, we focus on two major problems: no heat and inconsistent temperature.
No Heat
When the boiler produces no heat, it is a significant issue. Several factors could be the culprit.
- Thermostat settings: Ensure the thermostat is set correctly. It should be on “heat” mode.
- Power supply: Check if the boiler has power. Look at the circuit breaker and ensure it is on.
- Pilot light: If the boiler uses a pilot light, make sure it is lit. If not, relight it following the manufacturer’s instructions.
- Gas supply: Verify that the gas supply valve is open. A closed valve stops the gas flow, leading to no heat.
- Water level: Low water levels can prevent the boiler from heating. Refill the water if necessary.
Inconsistent Temperature
Inconsistent temperature can be frustrating. Several reasons can cause this problem.
- Thermostat location: The thermostat might be in a poor location. Avoid placing it near drafts or direct sunlight.
- Thermostat calibration: An incorrectly calibrated thermostat can cause temperature swings. Recalibrate or replace it if needed.
- Boiler size: A boiler that is too small or too large for the space can lead to inconsistent temperatures. Consider consulting a professional to determine the right size.
- System airlocks: Air trapped in the system can cause uneven heating. Bleed the radiators to remove airlocks.
- Circulator pump: A faulty circulator pump can cause uneven heat distribution. Check the pump and replace it if necessary.
Initial Checks
Performing initial checks on your Laars boiler can save time and money. Simple issues often cause boiler problems. Start with these basic checks before calling a professional.
Power Supply
Ensure the boiler has power. Check the circuit breaker. It should not be tripped. If tripped, reset it. If it trips again, there may be an issue. Verify the boiler switch is on. Sometimes, it gets turned off by mistake. Confirm the boiler is plugged in properly. Loose connections can cause problems.
Thermostat Settings
Check the thermostat. Ensure it is set to heat. The temperature should be set higher than the room temperature. Replace batteries if the thermostat is battery-operated. Make sure the thermostat is not in a drafty area. Drafts can affect readings and cause issues. Clean the thermostat if it is dusty. Dust can interfere with its function.
Check | Action |
---|---|
Power Supply | Confirm breaker, switch, and plug |
Thermostat Settings | Set to heat, check temperature, clean, replace batteries |
Performing these initial checks can help identify simple issues. It can save you from unnecessary service calls.
Error Codes
Understanding the error codes on your Laars Boiler can save you time and stress. These codes help identify specific issues, making troubleshooting easier and faster.
Decoding Codes
Each error code corresponds to a particular problem with the boiler. Here’s a quick guide to decode them:
Error Code | Description | Possible Cause |
---|---|---|
E01 | Ignition Failure | Check gas supply and ignition components |
E02 | Flame Loss | Inspect flame sensor and gas valve |
E03 | Overheat | Thermostat or circulation issues |
Reset Procedures
Resetting your boiler can often clear minor faults. Follow these steps to reset:
- Turn off the boiler using the power switch.
- Wait for at least 30 seconds.
- Turn the power back on.
- Check if the error code has cleared.
If the error persists, it may require professional service. Always consult the manual for specific reset instructions.

Credit: m.youtube.com
Water Pressure Problems
Understanding water pressure issues in Laars boilers can save time and money. Low or high pressure can lead to inefficiencies or system failures. Regular monitoring and maintenance of the boiler’s water pressure are crucial for optimal performance.
Pressure Gauge Reading
The pressure gauge shows the water pressure in your boiler. A typical Laars boiler should have a pressure reading between 1.0 and 2.0 bar. If the reading is outside this range, it indicates a problem.
Follow these steps to read the pressure gauge:
- Locate the pressure gauge on the boiler.
- Check the needle position.
- Ensure the pressure is within the recommended range.
If the needle is below 1.0 bar, the pressure is too low. If it is above 2.0 bar, the pressure is too high.
Repressurizing The System
If the pressure is low, you need to repressurize the system. Follow these steps:
- Turn off the boiler and let it cool.
- Locate the filling loop, usually found under the boiler.
- Attach the filling loop to the valves.
- Open both valves to allow water in.
- Watch the pressure gauge.
- Close the valves once the pressure reaches 1.5 bar.
If the pressure remains high, you may need to bleed the radiators. This releases trapped air and lowers the pressure.
Pressure Problem | Solution |
---|---|
Low Pressure (Below 1.0 bar) | Repressurize the system |
High Pressure (Above 2.0 bar) | Bleed the radiators |
Maintaining the correct pressure ensures your Laars boiler works efficiently. Regular checks can prevent future issues and costly repairs.
Pilot Light Issues
Experiencing issues with your Laars boiler’s pilot light can be frustrating. The pilot light is crucial for starting the boiler. When it fails, the boiler won’t work. Below, we discuss common pilot light issues and how to troubleshoot them.
Ignition Problems
One of the most common issues is ignition problems. These occur when the pilot light won’t ignite or stay lit. To troubleshoot:
- Check if the gas supply is on.
- Ensure the thermocouple is properly connected.
- Inspect the ignition system for dirt and debris.
If the ignition system is dirty, clean it carefully. Use a soft brush to remove debris. Make sure the ignition system is dry before trying to light the pilot again.
Flame Sensor Cleaning
The flame sensor detects if the pilot light is lit. If dirty, it may fail to detect the flame. Here’s how to clean the flame sensor:
- Turn off the boiler and let it cool.
- Locate the flame sensor, usually near the pilot light.
- Remove the flame sensor carefully.
- Clean the sensor with fine sandpaper.
- Reinstall the sensor and turn on the boiler.
Regular cleaning of the flame sensor can prevent pilot light issues. Aim to clean it every few months.
Issue | Possible Cause | Solution |
---|---|---|
Pilot light won’t ignite | Gas supply off | Turn on gas supply |
Pilot light won’t stay lit | Dirty thermocouple | Clean or replace thermocouple |
Pilot light goes out | Faulty flame sensor | Clean flame sensor |
Strange Noises
Strange noises from your Laars boiler can be alarming. Understanding these sounds helps in troubleshooting issues. Let’s explore some common noises you might hear.
Banging Sounds
Banging sounds usually indicate a problem with your boiler’s system. These noises often come from air trapped in the pipes. Air can cause water to bubble and create banging sounds.
- Check for air in the system.
- Bleed the radiators to release trapped air.
- Ensure the pump is working properly.
Another common cause is kettling. This happens when limescale builds up in the heat exchanger. The limescale restricts water flow, causing it to overheat and bang.
- Use a descaling product to remove limescale.
- Consider installing a water softener.
Whistling Noises
Whistling noises can be a sign of high water pressure. High pressure can cause water to flow too quickly, creating a whistling sound.
Possible Causes | Solutions |
---|---|
High water pressure | Reduce the pressure using the pressure relief valve. |
Blocked pipes | Check and clean any blockages. |
Another cause could be sludge build-up in the system. Sludge can restrict water flow, causing it to whistle.
- Flush the system to remove sludge.
- Use a chemical cleaner if necessary.
Regular maintenance can help prevent these issues. Always consult a professional if unsure.
Leak Detection
Detecting leaks in your Laars boiler is crucial. Leaks can lead to water damage and inefficiency. Proper leak detection ensures your boiler operates safely and efficiently.
Checking For Drips
Start by inspecting all visible pipes and connections. Look for any drips or wet spots.
- Check the area around the boiler for puddles.
- Feel the pipes for moisture.
- Inspect the pressure relief valve.
If you find any drips, mark the spots. This helps in identifying the source of the leak.
Fixing Leaks
Once you have identified the leaks, it’s time to fix them. Here are some steps:
- Turn off the boiler and let it cool.
- Tighten any loose connections using a wrench.
- Replace damaged gaskets or seals.
- Use plumber’s tape on threaded connections.
For persistent leaks, you may need to replace the faulty part. Always refer to the manufacturer’s manual for guidance.
Important: If you are not confident in performing these tasks, seek professional help.
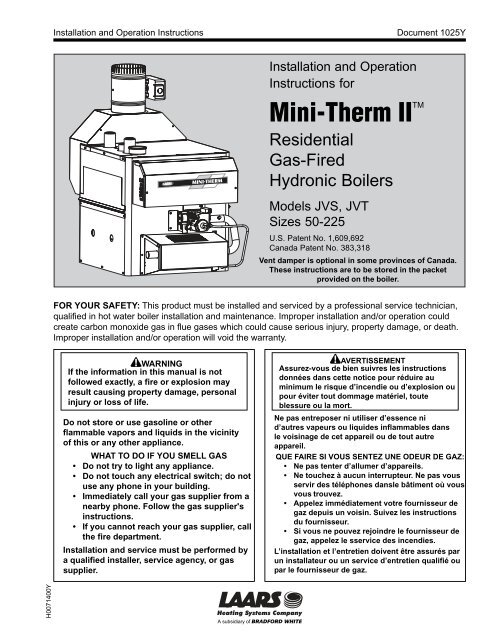
Credit: www.yumpu.com
Maintenance Tips
Proper maintenance ensures your Laars boiler operates efficiently. It prevents common issues and extends the unit’s lifespan. Follow these essential tips for optimal performance.
Regular Inspections
Regular inspections are crucial for identifying potential problems early. Conduct a visual check of your boiler every month. Look for any signs of leaks, rust, or unusual noises.
Here are some key areas to inspect:
- Check the water pressure gauge.
- Ensure the vents are clear of obstructions.
- Inspect the burner flame. It should be blue and steady.
- Look for any unusual odors around the unit.
Keep a record of your inspections. This helps track any changes or recurring issues.
Professional Servicing
Professional servicing is vital for comprehensive maintenance. Schedule an annual service with a qualified technician.
During the service, the technician will:
- Clean and inspect the heat exchanger.
- Check and calibrate the controls.
- Examine the flue and ventilation system.
- Test the gas pressure and adjust if needed.
- Inspect electrical connections and wiring.
A professional service ensures all components are in good working order. It also helps maintain the manufacturer’s warranty.
For easy reference, here is a summary of the key maintenance tips:
Maintenance Task | Frequency |
---|---|
Visual Inspection | Monthly |
Professional Servicing | Annually |
Regular maintenance keeps your Laars boiler running smoothly. It minimizes the risk of unexpected breakdowns and costly repairs. Follow these tips for a reliable and efficient heating system.
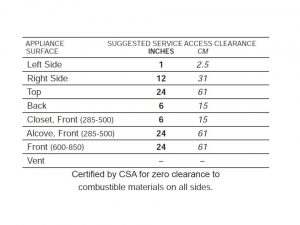
Credit: www.laarsboilersguide.com
Frequently Asked Questions
Why Is My Boiler Furnace Not Working?
Your boiler furnace might not be working due to thermostat issues, power supply problems, or a malfunctioning pilot light. Check for clogged filters, low water pressure, or faulty valves. Ensure regular maintenance for optimal performance.
What Is Troubleshooting In A Boiler?
Troubleshooting a boiler involves identifying and fixing issues causing malfunctions. Common problems include leaks, low pressure, and faulty thermostats. Regular maintenance helps prevent these issues. Ensure safety by turning off the boiler before inspecting. For complex problems, consult a professional technician.
What Is The Pressure On A Laars Boiler?
The pressure on a Laars boiler typically ranges between 12-15 psi when the system is cold. This ensures optimal performance.
How Do I Contact Laars?
Contact Laars by calling their customer support at 1-800-900-9276 or emailing them at techservice@laars. com. Visit their website for more details.
Conclusion
Troubleshooting your Laars boiler can save time and money. Regular maintenance helps avoid common issues. Always consult the manual for guidance. If problems persist, seek professional assistance. Proper care ensures your boiler runs efficiently. Stay proactive and keep your heating system in top condition.
Your comfort and safety are paramount.